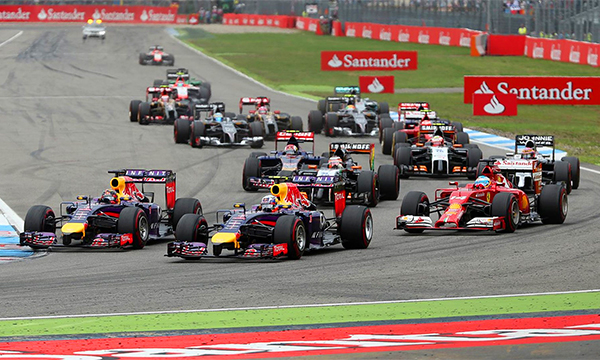
Люди за телевизором: что скрыто от зрителей Формулы-1
Старый чертежный прибор в углу, поношенный кожаный портфель и разбросанные карандаши - это рабочее место Эдриана Ньюи, главного конструктора Red Bull Racing. В сети про него ходит множество шуток: «он не лысый, а просто оптимизирует аэродинамику», «он единственный в мире, кто может видеть воздух». Его кульман - последний в Формуле-1 - остальные давно перешли на полностью компьютерное моделирование. И, кстати, на этом кульмане было начерчено четыре кубка конструкторов и четыре чемпионских титула подряд.
Формула-1. Миллиард глаз устремлен на пару гонщиков - пилотов любимой команды. Они - примы, звезды, им, в случае победы, достается вся слава. Вокруг спортсменов несколько раз за уикенд снуют техники команды пит-стопа. Эти 20 человек должны быть немыслимо быстры, чтобы выигрывать гонки, а значит, чем они лучше работают, тем короче их момент славы. Еще почти 40 человек в боксах следят за погодой, телеметрией, стратегией, запасными деталями, наконец - за бесперебойной работой оборудования. Они остаются в тени, лишь изредка попадая в объективы камер. Но есть еще несколько сотен человек, которые шанса на славу и публичность по сути лишены, несмотря на то, что куют будущие победы изо дня в день, без выходных, днем и ночью, даже за пределами гоночного сезона - речь о штаб-квартире Red Bull Racing.
В гости к «Красным быкам» мы приехали по приглашению компании Siemens PLM Software - не спонсора, но важнейшего технического партнера «конюшни». Их разработки - среда NX для автоматизированного проектирования и Teamcenter для общекомандной виртуальной рабочей среды - подобно нервной системе пронизывают весь организм команды. Наш гид - Алан Пислэнд - директор по техническому сотрудничеству. Он почти не бывает на гонках и признается, что победы создаются задолго до выхода болидов на трассу.
Когда смотришь телевизионные трансляции гонок, сложно представит, что в процессах принятия решений и обслуживания болидов участвуют люди, физически на трассе не присутствующие. На базе команды Red Bull Racing для этого есть отдельный зал, больше всего напоминающий центр управления полетами. Здесь в многоярусной аудитории в течение гоночного уикенда работают 30 человек, глаза которых устремлены на огромный экран 3,3 на 9,5 метра. Его разрешение настолько высокое, что вблизи он выглядит так же, как современные 4К телевизоры. И это не блажь - на него одновременно выводится вся телеметрия двух болидов, и графики обязаны быть кристально четкими. На фабрике шутят, что в свободное хотели бы устроить в этом зале кинотеатр, но на 30 мест будет слишком много желающих, да и начальство против.
Даже в те дни, когда гонки проходят на противоположном конце Земли, скажем, в Австралии, до городка Милтон Кинс данные долетают менее чем за 300 миллисекунд, при том, что за уикенд объем переданной информации достигает 400 Гб. Взаимодействовать с боксами им помогает система Siemens Teamcenter - единая среда, в которой хранятся все данные о проделанной командой работе, включая 3D-модели каждой из 7,5 тыс. уникальных деталей болидов, и все настройки машин. Все это одновременно доступно инженерам и на базе, и на трассе.
На этом этапе к работе шести десятков человек во время уикенда добавляется труд еще 60 работников R&D департамента на заводе в Милтон Кинз. Все детали, попадающие на трассу, сначала проходят через их руки. Каждую неделю специалисты при помощи 3D-печати создают на высокоточных принтерах тысячи моделей (в 60% масштабе, согласно требованиям FIA) для продувки в аэродинамической трубе. Заправить материалом самый маленький из них стоит более 5 млн рублей. Затем каждую из деталей ждет измерение по более чем четырем сотням параметров, и лишь самые удачные модели пойдут в производство. На фабрике говорят, что в современной Формуле-1 нет места догадкам - этот спорт основывается на точных данных.
Однако даже еще раньше детали, не выходя за пределы компьютера, проверяют на симуляторе: «разбивают» в виртуальных краш-тестах и «продувают» в цифровой системе CFD (вычислительная гидродинамика). Для этого у команды есть собственный суперкомпьютер, точных параметров которого не рассекречивают, но упоминают, что он способен хранить более петабайта данных (1 тыс. терабайт), каждую секунду обрабатывая и записывая по 200 Мб информации. Эту систему для команды создали компании IBM, отвечавшая за сам суперкомпьютер, и Ansys - за алгоритмы симуляции. Модели для просчетов поставляются прямо из среды моделирования NX, и все вместе прочно «завязано» на систему Teamcenter. Однако, рассказывает Алан, какими бы точными не были измерения, финальное слово за проверками на трассе. Именно по данным с тестов, даже если они расходятся с симуляцией, калибруются все приборы: в конце концов, в гонке пилотам работать именно с этими деталями.
Тысяча обновлений в неделю, 30 тыс. за сезон, но снова это лишь верхушка айсберга. Ведь эти десятки тысяч - лишь утвержденные проекты, которым был дан «зеленый свет». На самом деле, департамент дизайна, отвечающий за разработку новинок и состоящий из 110 человек, работающих в уходящем за горизонт опенспейсе, генерирует намного больше идей. Количество проектов, отвергнутых в процессе рассмотрения, похоже, плохо поддается подсчету. Кстати, многие из разработок начинаются с оцифровки бумажных чертежей Эдриана Ньюи - на фабрике говорят, что такой человек может позволить себе работать так, как ему удобно, а остальные могут подстроиться.
Изготовлением деталей, которые придуманы и проверены предыдущими департаментами, в команде Red Bull Racing занимается отдел с еще большим штатом - в 240 человек. Даже несмотря на то, что разработки на пути к производству проходят жесточайшую селекцию, а количество шасси ограничено пятью на год, эти ребята за гоночный сезон создают более 48 тыс. различных деталей, ведь команда почти все, за исключением моторов, старается делать сама. В этом им помогает пять автоклавов, чьи двери в процессе работы испытывают нагрузку в 600 тонн, и 22 пятиосевых фрезерных станка. В качестве сырья используется более 50 сортов углеволокна с различными узорами плетения и варьирующейся толщиной, 60 различных типов металлического сырья - от обычных сталей и алюминия до магниевых сплавов, титана и таких экзотических материалов, как матричный металлический композит или сплав Densamet, более тяжелый, чем золото, свинец или вольфрам и вплотную приближающийся по этому показателю к отработанному урану.
Скорость нужна не только в гонке - чтобы обеспечить ее, начинать необходимо со скорости на производстве: несмотря на то, что в норме путь детали из-под пера инженера до трассы занимает пять дней, часто бывает, что элемент, одобренный для производства утром, изготавливают днем, а вечером он уже летит на трассу. Для обеспечения такого уровня гибкости сами инструменты производства зачастую разрабатываются с нуля прямо здесь, с использованием все того же пакета Siemens NX.
И ни в коем случае нельзя забывать о том, что все это необходимо отполировать, покрасить и собрать. Разумеется, после тщательной проверки. Дело в том, что инспекции подвергается 100% произведенных деталей: каждый винтик тщательно измеряют точнейшими цифровыми приборами, чтобы он в точности соответствовал проекту инженера. Окрашиваются детали, кстати, по новой технологии - если раньше на болиды клеили наклейки прямо поверх краски, то теперь вся ливрея целиком покрывается лаком - аэродинамика зависит даже от таких мелочей. А матовая краска, которой в этом сезоне щеголяют машины «Быков», напротив, на сопротивление воздуху не влияет. Нередки случаи, когда ради скорости доставки краску наносят уже в самолете, по дороге на трассу.
В итоге от начала разработки нового болида до его появления на свет проходит всего пять месяцев: ничтожно мало по меркам автомобилестроения. Уже сейчас по коридорам фабрики ездят тележки с деталями, на которых красуется недвусмысленная маркировка RB13. В помещении, где механики проводят финальную сборку болидов, каждый из которых состоит из 100 000 деталей, и которое полностью повторяет планировку боксов Red Bull Racing на большинстве гоночных трасс, стоит шасси RB12, но колеса на нем установлены огромные - такие появятся на болидах только в следующем сезоне, но пит-топы тренировать надо уже сейчас.
Итак, на арене в течение гоночного сезона находится команда Red Bull Racing: два гонщика, 58 человек в боксах. А за кулисами - 640 сотрудников на фабрике, 8 670 часов работы суперкомпьютера, 30 тыс. обновлений деталей, 48 тыс. изготовленных запчастей для пяти шасси, 45 тонн груза, перемещающегося вместе с командой с трассы на трассу, 8 400 гигабайт данных, переданных в операционный центр из боксов. И все это функционирует для того, чтобы к концу сезона автомобиль начал проезжать круг трассы на секунду быстрее, чем в начале года. Но одна секунда в мире Формулы-1 - это целая пропасть.
Борис Ульзибат, специально для Autonews.ru
Фото: Red Bull
Формула-1. Миллиард глаз устремлен на пару гонщиков - пилотов любимой команды. Они - примы, звезды, им, в случае победы, достается вся слава. Вокруг спортсменов несколько раз за уикенд снуют техники команды пит-стопа. Эти 20 человек должны быть немыслимо быстры, чтобы выигрывать гонки, а значит, чем они лучше работают, тем короче их момент славы. Еще почти 40 человек в боксах следят за погодой, телеметрией, стратегией, запасными деталями, наконец - за бесперебойной работой оборудования. Они остаются в тени, лишь изредка попадая в объективы камер. Но есть еще несколько сотен человек, которые шанса на славу и публичность по сути лишены, несмотря на то, что куют будущие победы изо дня в день, без выходных, днем и ночью, даже за пределами гоночного сезона - речь о штаб-квартире Red Bull Racing.
В гости к «Красным быкам» мы приехали по приглашению компании Siemens PLM Software - не спонсора, но важнейшего технического партнера «конюшни». Их разработки - среда NX для автоматизированного проектирования и Teamcenter для общекомандной виртуальной рабочей среды - подобно нервной системе пронизывают весь организм команды. Наш гид - Алан Пислэнд - директор по техническому сотрудничеству. Он почти не бывает на гонках и признается, что победы создаются задолго до выхода болидов на трассу.
Когда смотришь телевизионные трансляции гонок, сложно представит, что в процессах принятия решений и обслуживания болидов участвуют люди, физически на трассе не присутствующие. На базе команды Red Bull Racing для этого есть отдельный зал, больше всего напоминающий центр управления полетами. Здесь в многоярусной аудитории в течение гоночного уикенда работают 30 человек, глаза которых устремлены на огромный экран 3,3 на 9,5 метра. Его разрешение настолько высокое, что вблизи он выглядит так же, как современные 4К телевизоры. И это не блажь - на него одновременно выводится вся телеметрия двух болидов, и графики обязаны быть кристально четкими. На фабрике шутят, что в свободное хотели бы устроить в этом зале кинотеатр, но на 30 мест будет слишком много желающих, да и начальство против.
Даже в те дни, когда гонки проходят на противоположном конце Земли, скажем, в Австралии, до городка Милтон Кинс данные долетают менее чем за 300 миллисекунд, при том, что за уикенд объем переданной информации достигает 400 Гб. Взаимодействовать с боксами им помогает система Siemens Teamcenter - единая среда, в которой хранятся все данные о проделанной командой работе, включая 3D-модели каждой из 7,5 тыс. уникальных деталей болидов, и все настройки машин. Все это одновременно доступно инженерам и на базе, и на трассе.
На этом этапе к работе шести десятков человек во время уикенда добавляется труд еще 60 работников R&D департамента на заводе в Милтон Кинз. Все детали, попадающие на трассу, сначала проходят через их руки. Каждую неделю специалисты при помощи 3D-печати создают на высокоточных принтерах тысячи моделей (в 60% масштабе, согласно требованиям FIA) для продувки в аэродинамической трубе. Заправить материалом самый маленький из них стоит более 5 млн рублей. Затем каждую из деталей ждет измерение по более чем четырем сотням параметров, и лишь самые удачные модели пойдут в производство. На фабрике говорят, что в современной Формуле-1 нет места догадкам - этот спорт основывается на точных данных.
Однако даже еще раньше детали, не выходя за пределы компьютера, проверяют на симуляторе: «разбивают» в виртуальных краш-тестах и «продувают» в цифровой системе CFD (вычислительная гидродинамика). Для этого у команды есть собственный суперкомпьютер, точных параметров которого не рассекречивают, но упоминают, что он способен хранить более петабайта данных (1 тыс. терабайт), каждую секунду обрабатывая и записывая по 200 Мб информации. Эту систему для команды создали компании IBM, отвечавшая за сам суперкомпьютер, и Ansys - за алгоритмы симуляции. Модели для просчетов поставляются прямо из среды моделирования NX, и все вместе прочно «завязано» на систему Teamcenter. Однако, рассказывает Алан, какими бы точными не были измерения, финальное слово за проверками на трассе. Именно по данным с тестов, даже если они расходятся с симуляцией, калибруются все приборы: в конце концов, в гонке пилотам работать именно с этими деталями.
Тысяча обновлений в неделю, 30 тыс. за сезон, но снова это лишь верхушка айсберга. Ведь эти десятки тысяч - лишь утвержденные проекты, которым был дан «зеленый свет». На самом деле, департамент дизайна, отвечающий за разработку новинок и состоящий из 110 человек, работающих в уходящем за горизонт опенспейсе, генерирует намного больше идей. Количество проектов, отвергнутых в процессе рассмотрения, похоже, плохо поддается подсчету. Кстати, многие из разработок начинаются с оцифровки бумажных чертежей Эдриана Ньюи - на фабрике говорят, что такой человек может позволить себе работать так, как ему удобно, а остальные могут подстроиться.
Изготовлением деталей, которые придуманы и проверены предыдущими департаментами, в команде Red Bull Racing занимается отдел с еще большим штатом - в 240 человек. Даже несмотря на то, что разработки на пути к производству проходят жесточайшую селекцию, а количество шасси ограничено пятью на год, эти ребята за гоночный сезон создают более 48 тыс. различных деталей, ведь команда почти все, за исключением моторов, старается делать сама. В этом им помогает пять автоклавов, чьи двери в процессе работы испытывают нагрузку в 600 тонн, и 22 пятиосевых фрезерных станка. В качестве сырья используется более 50 сортов углеволокна с различными узорами плетения и варьирующейся толщиной, 60 различных типов металлического сырья - от обычных сталей и алюминия до магниевых сплавов, титана и таких экзотических материалов, как матричный металлический композит или сплав Densamet, более тяжелый, чем золото, свинец или вольфрам и вплотную приближающийся по этому показателю к отработанному урану.
Скорость нужна не только в гонке - чтобы обеспечить ее, начинать необходимо со скорости на производстве: несмотря на то, что в норме путь детали из-под пера инженера до трассы занимает пять дней, часто бывает, что элемент, одобренный для производства утром, изготавливают днем, а вечером он уже летит на трассу. Для обеспечения такого уровня гибкости сами инструменты производства зачастую разрабатываются с нуля прямо здесь, с использованием все того же пакета Siemens NX.
И ни в коем случае нельзя забывать о том, что все это необходимо отполировать, покрасить и собрать. Разумеется, после тщательной проверки. Дело в том, что инспекции подвергается 100% произведенных деталей: каждый винтик тщательно измеряют точнейшими цифровыми приборами, чтобы он в точности соответствовал проекту инженера. Окрашиваются детали, кстати, по новой технологии - если раньше на болиды клеили наклейки прямо поверх краски, то теперь вся ливрея целиком покрывается лаком - аэродинамика зависит даже от таких мелочей. А матовая краска, которой в этом сезоне щеголяют машины «Быков», напротив, на сопротивление воздуху не влияет. Нередки случаи, когда ради скорости доставки краску наносят уже в самолете, по дороге на трассу.
В итоге от начала разработки нового болида до его появления на свет проходит всего пять месяцев: ничтожно мало по меркам автомобилестроения. Уже сейчас по коридорам фабрики ездят тележки с деталями, на которых красуется недвусмысленная маркировка RB13. В помещении, где механики проводят финальную сборку болидов, каждый из которых состоит из 100 000 деталей, и которое полностью повторяет планировку боксов Red Bull Racing на большинстве гоночных трасс, стоит шасси RB12, но колеса на нем установлены огромные - такие появятся на болидах только в следующем сезоне, но пит-топы тренировать надо уже сейчас.
Итак, на арене в течение гоночного сезона находится команда Red Bull Racing: два гонщика, 58 человек в боксах. А за кулисами - 640 сотрудников на фабрике, 8 670 часов работы суперкомпьютера, 30 тыс. обновлений деталей, 48 тыс. изготовленных запчастей для пяти шасси, 45 тонн груза, перемещающегося вместе с командой с трассы на трассу, 8 400 гигабайт данных, переданных в операционный центр из боксов. И все это функционирует для того, чтобы к концу сезона автомобиль начал проезжать круг трассы на секунду быстрее, чем в начале года. Но одна секунда в мире Формулы-1 - это целая пропасть.
Болид Red Bull Racing RB12 в цифрах
- Масса - 702 кг
- Максимальная Мощность силовой установки - 760 л.с. / 15 000 об/мин
- Перегрузки при разгоне - 1,5 G
- Перегрузки в поворотах - 5,5 G
- Перегрузки при торможении - до 7,0 G
- Прижимная сила на максимальной скорости - 2106 кг
Борис Ульзибат, специально для Autonews.ru
Фото: Red Bull